1.Mixing: Metal powder and binder are mixed in a certain proportion to form a uniform feedstock. The binder used in MIM technology has the function of enhancing powder flow and maintaining the shape of the feedstock.
2.Injection molding: The feedstock is injected into the mold at high temperature, pressure, and speed. The feedstock flows into the mold cavity through the gate (the number of mold cavities is designed according to the structural characteristics of the product to improve production efficiency), and after compacting and cooling, an injection blank is formed. The blank has a certain strength and density. In the design of the mold cavity for new materials, the shrinkage ratio of the blank after sintering should be considered. The shrinkage ratio varies according to the material composition.
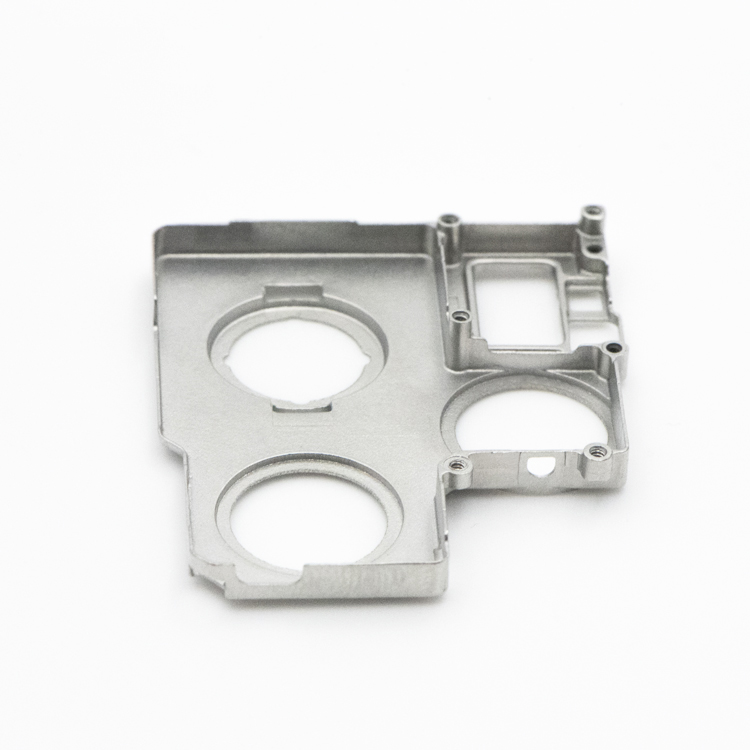
3. Debinding: After debinding, 98% of the binder in the green compact will be removed, leaving only 2% to maintain the shape. When the green compact is debound, the metal powder injection molding manufacturer will take a sample for destructive testing. If the powder is relatively loose when the compact is cut, it indicates that the debinding is qualified. If there are agglomerates when cut, it indicates that the debinding standard has not been reached.
4. Sintering: Sintering for 24 hours, the remaining 2% binder is completely removed, and the sintered product has high density and good mechanical and physical properties. After sintering, processing is also part of the process for manufacturing mobile phone parts using metal powder injection molding (MIM).
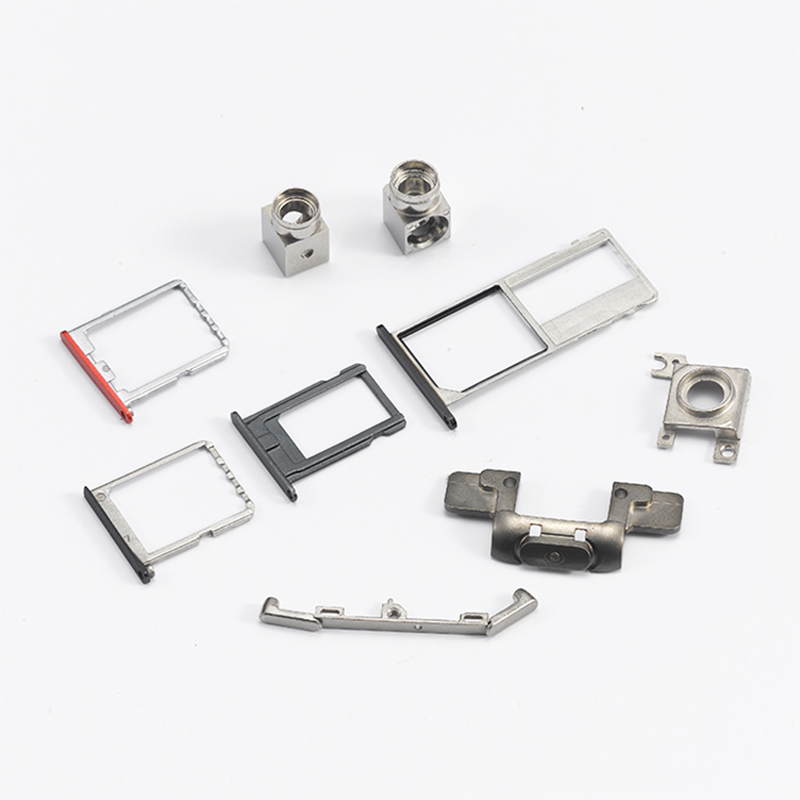
With the development of the economy, the market now demands lighter, thinner, and more aesthetically pleasing phones. Advanced metal powder injection molding (MIM) technology is required to reduce the size and weight of phone components. MIM is suitable for manufacturing MIM phone parts.