Which mobile phone parts will require the MIM process?
The applications of MIM process in mobile phones, at present, are metal tray of SIM card , volume buttons, mobile phone interface, camera frame, hinge, lifting camera precision parts, dual camera triple camera precision parts, gears and so on.
1.Metal Frame of Phone Camera System
A camera is a must for every mobile phone, but the structure of metal frame of phone camera system is more precise, the performance requirements are relatively high. Therefore, the ordinary production process is difficult to produce and the production cost is high. MIM can form a variety of precision metal parts at one time, with few processing steps, fast forming, high material utilization, mass production, and efficient production of mobile phone camera brackets.
Having more cameras in a phone means that the lens, sensor, LED flash and other components should be firmly and safely assembled together, and the bracket of the camera ring should be thinner. However, in order to meet these requirements, the wall thickness, flatness, and contour of the product must also be improved. MIM process can solve these problems easily.
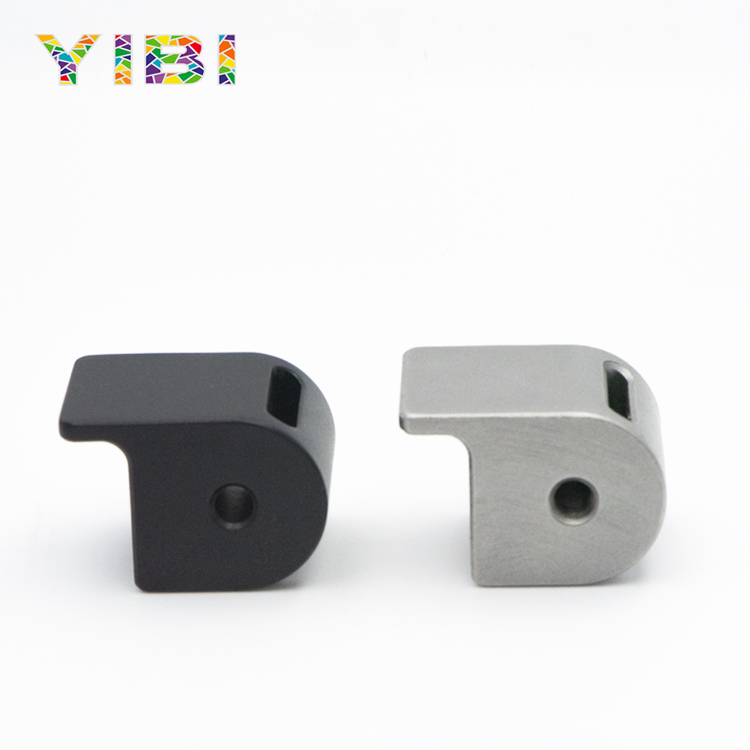
2.Folding Screen Hinge
The cores of folding screen mobile phones are the hinges at the folding places of the two screens, which determines the success of the folding screen. In addition to the foldable and thin design, the central core component hinges also needs to be light, flexible, thin, and reliable. The requirements for accuracy of rotation and friction coefficient are particularly high. MIM process is very suitable to ensure stability. sex and intensity.
3.Metal Tray of SIM Card
Since the mobile phone has changed from a detachable battery to the current non-detachable structural design, there is an additional design on the mobile phone: SIM card tray. Making the card tray pop up automatically under the elastic action of the pop-up mechanism, can save space and achieve a elegant operation. Therefore, the manufacturing precision of the mobile phone card tray is required to be very high, and it also needs to have advantages in performance such as density, structural density, and wear resistance. MIM process is unanimously considered to be a very suitable molding technology for the production of SIM card trays.
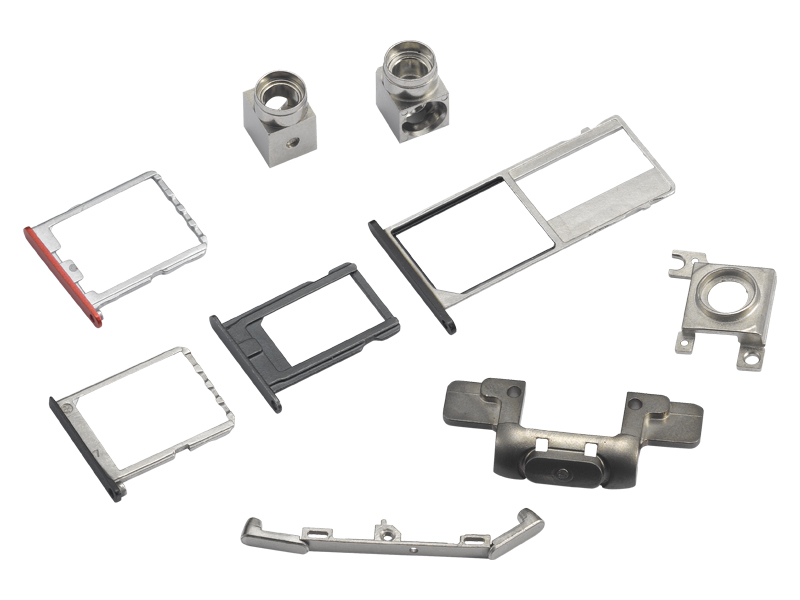
4. Mobile phone lifting camera
In recent years, mobile phone users' pursuit of screen ratio has reached its peak, so designers have tried their best to break through the bottleneck of 100% full screen. The invention of the lifting camera not only optimizes the appearance of the screen, but also the mechanical control of one up and one down is full of sense of technology. In order to realize the lifting function of the camera, the inside of the camera needs the support of micro precision components such as screw rods and slide rails, and these parts need to be produced by MIM process, which can not only be mass-produced, but also ensure the high quality of precision parts. Moreover, the production cost is lower than the traditional process.